The composition and structural characteristics of PTFE determine that it has the characteristics of high and low temperature resistance, corrosion resistance, weather resistance, high lubrication, non-adhesion, etc., but there are also low hardness, large coefficient of linear expansion, poor thermal conductivity, poor mechanical properties, poor wear resistance, poor creep resistance, easy cold flow, secondary processing difficulties and other shortcomings, to a certain extent, limiting its wide application. Therefore, the research on its modification has been a hot topic.
The modification methods of PTFE mainly include surface modification, blending modification, filling modification and chemical modification. Among them, filling and blending modified PTFE is a simple and effective method.
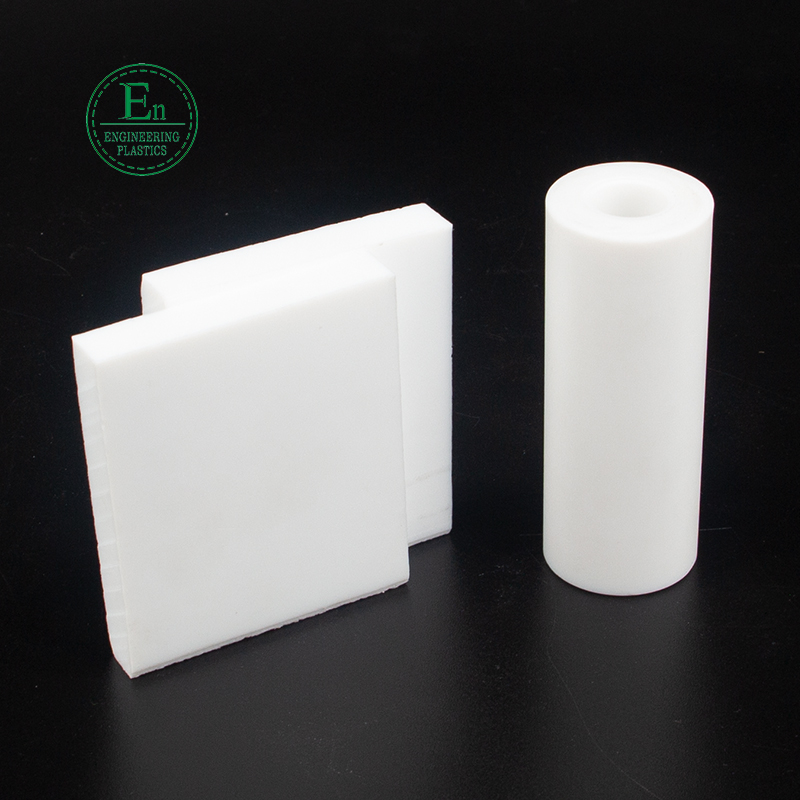
01
Inorganic filler filling modification
Commonly used inorganic fillers are nanoparticle fillers, metal and oxide fillers, whisker fillers and graphite, carbon fiber (CF), glass fiber (GF) and so on.
Nanoparticle packing
The nanoparticle has the characteristics of small size, large specific surface area, and large interface area and interaction with the polymer, so the composite of the nanoparticle and the polymer can obtain the ideal interface adhesion. In addition, nanoparticles can also eliminate the mismatch between the thermal expansion coefficients of the two components and bind the interchain motion of PTFE macromolecules, which is conducive to improving the tribological and mechanical properties of the polymer. At present, nano-materials used to fill PTFE mainly include nano-al2o3, SiO2 and TiO2.
Metal and oxide filler fill
Metal packing has good thermal conductivity, as well as wear resistance and many other excellent properties. Adding metal filler to PTFE can not only significantly improve the thermal conductivity of PTFE, but also greatly improve its wear resistance. For example: Cu particles, Al2O3 fibers and so on.
Whisker packing
Whiskers are single crystal fibers with few defects, usually only a few microns in diameter. Its high mechanical strength, tensile strength close to the theoretical strength of pure crystal, can be widely used to enhance the performance of composite materials, is a promising new material.
Whisker materials are four needle-like zinc oxide whisker, calcium sulfate whisker and so on.
Other packing
Other fillers are graphite, CF, GF and so on. CF, GF and graphite can be filled individually or cooperatively. It is found that the cooperatively reinforced PTFE composite exhibits plastic fracture when stretched, and is a high-performance lubricating sealing material with good comprehensive mechanical properties.
02
Polymer blending modification
The friction coefficient of PTFE composites formed by inorganic filling is usually large, and the damage to the grinding parts is large, and the mechanical properties of the products are not high enough. Polymer blending modified PTFE obviously improved the above shortcomings. The main organic polymers used to fill PTFE are
Polyphenylene Sulfide (PPS), polyether ether ketone (PEEK), polyimide (PI) and polyphenyl ester (POB).
For example, PEEK/PTFE composites are prepared by hot die pressing process and used as composite bearing materials. The results show that the friction coefficient of the composite decreases significantly with the increase of PTFE content, and the life of the bearing material is prolonged.
Some scholars have prepared PPS /PTFE, PI /PTFE, PEEK/PTFE, POB/PTFE, aramid /PTFE and other 5 kinds of composite materials. It was found that PTFE composites with 15% polyphenyl ester (POB) had the best anti-friction effect, and PTFE composites with 15%PI had the best wear resistance. In contrast, PTFE composite filled with 15% aramid has the best friction and wear properties and mechanical properties, and its wear resistance is nearly 400 times higher than that of pure PTFE, while the friction coefficient is only 84% of that of pure PTFE.