Carbon fiber composite material is a material composed of many carbon fiber tows arranged in a certain direction, and then they are mixed and connected with a matrix such as resin, ceramic, and metal. Compared with traditional metal materials, carbon fiber composite materials have the advantages of low density, high specific strength/specific stiffness, corrosion resistance, fatigue resistance, high temperature resistance, easy design, and easy large-area integral molding processing.
Today, the market for 3D printed carbon fiber composite materials has begun to make efforts in mass production. Arris Composites has cooperated with Airbus to conduct composite material research to reduce cabin supports.
Sustainable development prospects
There are three major trends in the development of 3D printing of composite materials. First, we will see the industrialization of processes and systems, and the combination of hardware and software development will more support mass production. The second is to perform more sensor control on the system to achieve real-time process control-thermal, size and optical sensing can improve process tolerances. The third is that the new software used to improve the efficiency of 3D printing operations (for example, pre-processing workflow, job management, etc.) is more mature, so as to be more in-depth for the new design and simulation of multi-material parts.
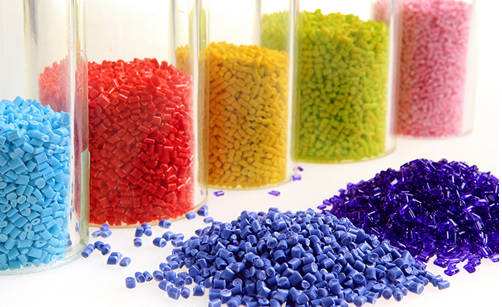
Sustainable Air Travel Industry Development
Arris Composites from California, USA, revealed a research project with Airbus, which focuses on the production of cabin supports. The project aims to significantly reduce aviation emissions by using innovative manufacturing methods and materials (including composite materials).
According to Arris Composites, replacing the metal bracket (220 grams) with topology-optimized, aligned continuous fiber composite parts (50 grams) reduced the weight by more than 75%. The reduction in weight also translates into highly optimized fuel savings, because hundreds of these supports are part of an aircraft.
If you look at the weight reduction from a larger perspective, the significance of weight reduction is even greater. If 100 airplanes are manufactured a year, each airplane is equipped with 500 brackets, plus 50,000 lighter weight brackets. Save 113 million metric tons of fuel during the entire life cycle of the aircraft and reduce 357 million metric tons of carbon dioxide emissions.
According to Airbus, bionic design, topology optimization design and advanced composite materials are the future. Arris Composites combines the advantages of 3D printing with the advantages of composite materials and is helping the industry to combine these designs and material ideals to create a flying future .
In addition, Arris Composites' additive molding technology combines additive manufacturing and high-speed compression molding processes, which will have a huge impact on replacement parts and future aircraft structures, proving that it is possible to reduce carbon emissions. Airbus itself is committed to exploring such technological approaches to support the vision of more sustainable air travel for future generations.